«Алмазная сталь»
Тамахаганэ, или «алмазная сталь», - легендарная сталь, окруженная мифами и легендами. На протяжении веков секреты обработки тамахаганэ знали только кокадзи - кузнецы, посвященные в таинства работы с алмазной сталью.
Получить тамахаганэ можно было в традиционных плавильных печах - татара. Они, как и другие плавильные печи, использовали способность раскаленного железа объединяться с углеродом, в результате чего получалась сталь. Особенностью татары было то, что перед каждой новой плавкой ее приходилось отстраивать заново: чтобы извлечь полученную в конце плавки сталь, нужно разрушить ее стены. Эта печь не является исконно японским изобретением, видимо, она была заимствована на рубеже VI-VII вв. из Маньчжурии, но уже в IX в. печи татара были широко распространены по всей Японии.
Железная руда в префектуре Симанэ, традиционной области производства тамахаганэ, встречалась в форме сатэцу, или черного (железного) песка. Сатэцу - продукт распада естественных залежей железной руды, его можно было найти рядом с руслами рек. Собранная песчаная смесь содержала не более одного процента железа, поэтому ее обогащали при помощи промывки в специальных водяных каналах с волнистыми препятствиями на дне. Во время движения по ним более тяжелые частички железа оседали, а порода вымывалась.
Для получения тамахаганэ в процессе одной плавки в печь загружают около 8 тонн обогащенного сатэцу и около 13 тонн древесного угля, что обеспечивает получение необходимого количества углерода. В татаре расплавленное железо соединяется с углеродом от сжигаемого древесного угля.
Процесс получения алмазной стали начинался с постройки новых глиняных стен (толщиной не менее 30 см) на печи татара. Затем на дне печи разводили огонь, куда на протяжении нескольких часов подбрасывали древесный уголь и куски дуба. Когда ко-кадзи решал, что угли готовы (как правило, при температуре 1200-1500 °С), их покрывали слоем сатэцу, а сверху снова посыпали древесным углем. Через полчаса в печь опять добавляли сатэцу, покрыв его новым слоем древесного угля. Так на протяжении трех дней. В течение всего этого времени, пока мастер следил за добавлением сатэцу и древесного угля, его помощники раздували кузнечные мехи. Столь долгий и утомительный процесс был нужен для достаточного насыщения железа углеродом.
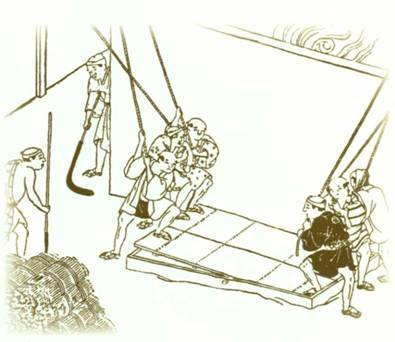
Огонь в традиционной японской татаре поддерживали сразу несколько мастеров. Иллюстрация из книги Адольфа Ледебура «Сталь и чугун», 1901 г.
Обычно производством тамахаганэ занимались зимой, когда к работе можно было привлечь отдыхающих от полей крестьян. Через три дня на дне татара образовывался стальной блок, или кэ-ра, весом около двух тонн. Для его извлечения стены татара приходилось разрушить. Итого весь процесс выплавки занимал около пяти дней: один день на постройку татары, три дня на выплавку кэра и еще один день - на извлечение выплавленного железа из печи. Но на этом производство тамахаганэ еще не заканчивалось. Неоднородный по своей структуре кэра еще нужно было раздробить на более мелкие части, более однородные по содержанию углерода. Для этого массивный слиток затягивался на вершину обрыва и сбрасывался на камни, после чего полученный материал сортировался и проходил последующее дробление. Но порой слитки кэра выходили такого огромного размера, что сил рабочих просто не хватало для того, чтобы просто сдвинуть такой слиток с места. По всей Японии сохранились татара с оставшимися в них слитками кэра, которые так и не смогли использовать.
Около половины полученного таким образом металла составляет сталь с высоким содержанием углерода (от 0,6-0,8 % до 1,5-1,7 %). Для дальнейшего создания клинка наиболее оптимальной считалась сталь с содержанием углерода 1-1,2 %. Именно она и называется тамахаганэ.
Сегодня, как и много веков назад, «алмазная сталь» изготавливается в традиционных печах японского типа татара, в небольшом городке в префектуре Симанэ на западе Хонсю, на побережье Японского моря, на протяжении веков остающемся центром производства тамахаганэ. С одной лишь разницей, что мехи приводятся в движение не мускульной силой человека, а электродвигателем.
Но вот от способа добычи и обогащения сатэцу путем нагнетания его в водяные каналы с ребрами для задержания более тяжелых частиц железа отказались. Сатэцу сегодня добывается современными способами: песчаная порода собирается бульдозером, а металлические частицы извлекаются из нее с помощью мощного магнита.
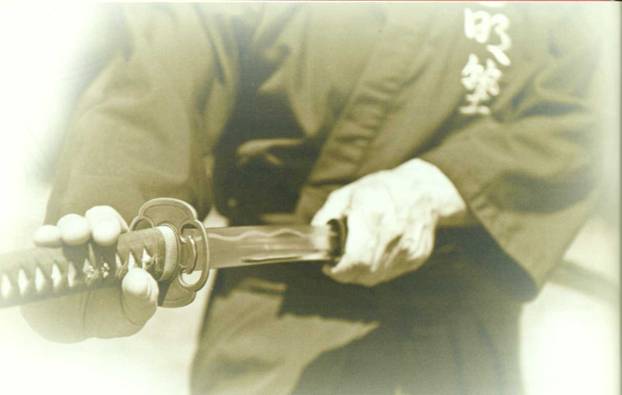
Несокрушимые самурайские мечи изготавливались из тамахаганэ
После предварительной сортировки тамахаганэ попадает к ко-кадзи, который проводит ее дополнительную сортировку. Так, для выковывания каваганэ (сталь для наружной поверхности лезвия клинка) понадобится 5-6 кг тамахаганэ с высоким содержанием углерода, так как в процессе ковки произойдет значительная его потеря. Куски такой тамахаганэ будут плотными и тяжелыми, с ярко выраженным серебристым цветом. Куски же серо-черного цвета содержат меньший процент углерода и могут быть использованы для производства более мягкой сердцевины клинка, называемой синганэ. После сортировки тамахаганэ нагревают в кузнечном горне и расковывают в плоские пластины.
Для создания одного клинка требуется около 6 кг тамахаганэ (именно такое количество необходимо кузнецу для изготовления одного килограмма стали для клинка). При цене от $50 за килограмм тамахаганэ только цена на материал для изготовления одного клинка составит около $300.
доспехи рыцаря своими руками |
реактивный конвертоплан |
в 1748 изобретение |
история создания аэростата для детей |